A Concerted Effort to Counter the Supply Chain Crisis
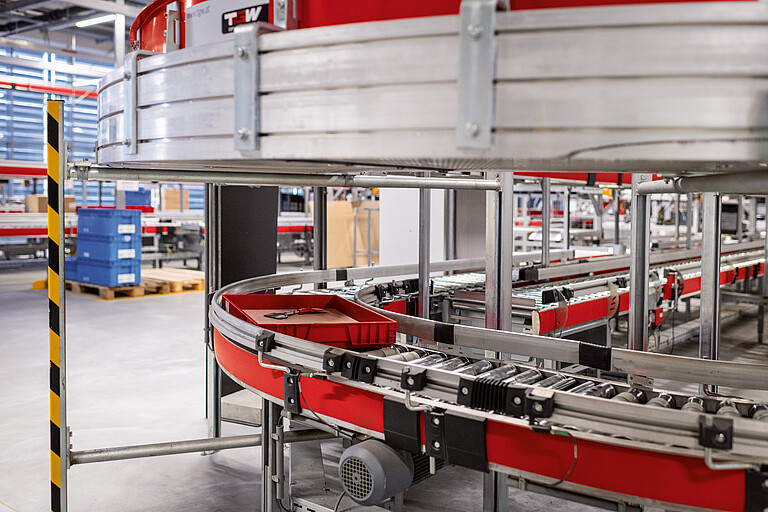
Production bottlenecks caused by the COVID-19 pandemic, steep price increases for materials and higher transport costs: Global supply chains are under pressure as never before, not least due to the effects of the war in Ukraine.
2023 became a year of records – negative records: Lowest availability ever, highest inventory ever, highest airfreight costs ever, highest number and value of backorders ever. Despite all these challenges, the Hilti team did everything possible to ensure product availability for our customers at all times. “We have massively built up inventory ‘on the water’ and in our warehouses to counter supply chain problems. At peak times, we have ramped this up to around a billion Swiss francs,” says Roeland Baaijens, Global Head of Logistics. As a result, we secured orders more than 60 days in advance for the products we had available in the warehouse. At the same time, we also faced the highest number of out-of-stock items in the history of Hilti.
We have massively built up inventory ‘on the water’ and in our warehouses to counter supply chain problems. At peak times, we have ramped this up to around a billion Swiss francs.
Roeland Baaijens, Global Head of Logistics
TRADE ROUTES UNDER STRESS
Supply chains are currently under pressure as never before. There are many reasons for this. As a result of the war in Ukraine, the global economy is suffering, primarily from high prices for energy, raw materials and foodstuffs. But the disruptions to trade routes that have existed since the pandemic also continue to strain existing systems. In addition, uncertainty continues to grow on the markets as experts forecast a decline in global economic growth for 2023.
A dynamic market environment requires flexible processes. Hilti therefore launched the MOVE initiative to improve transport management. In 2022, for example, a tracking system was introduced to automatically monitor container shipments sent via sea freight with the SAP system. Additionally, a transport management system ensures that the best carrier, offering the best service and cost balance, is automatically selected for each customer order. Furthermore, the procurement team is protecting itself against supply shocks by increasing the number of alternative suppliers and manufacturing Hilti products at additional sites, explains Baaijens. For example, the plant in Mexico is now being expanded to include more product lines.
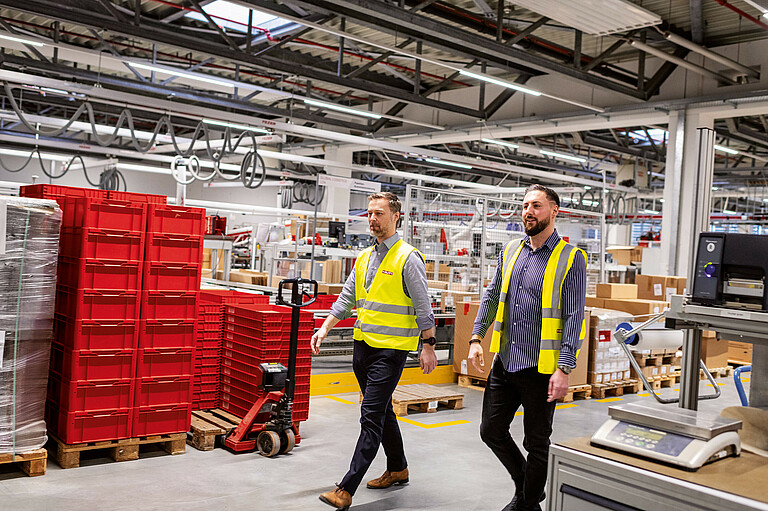
NEW BATTERY SYSTEM
Nowhere were the challenges facing the global supply chain harder or more evident than in the launch of our new Nuron battery platform. “To execute the largest product launch in the history of Hilti despite plant closures, transportation disruptions and rising costs in 2022 was not easy,” recalls Ted Przybylowicz, Head of Power Tools and Accessories. With more than 70 new products launched simultaneously, first in North America in March and then starting in Europe in September, “bringing Nuron home required close collaboration across the whole organization, including the markets, global logistics, business units and our plants.”
There are increasing signs that supply chain processes will significantly improve soon. Hilti’s answer to this is called Operation Soft Landing: “We have to manage down our inventory in a controlled way, in which we reduce lead times in line with the actual transport times,” says Roeland Baaijens. This is a joint effort between Global Logistics, Supply and Finance. At the same time, supply chains at Hilti are becoming more segmented, which we want to couple with highly efficient supply processes and active cross-functional teamwork. This goes toward ensuring that the customers’ supply is always guaranteed, no matter which products are being ordered.
Close collaboration leads to better experiences. Discover how with Lead 2030 Hilti is Making Construction Better.