Better Applications
Reaching New Heights
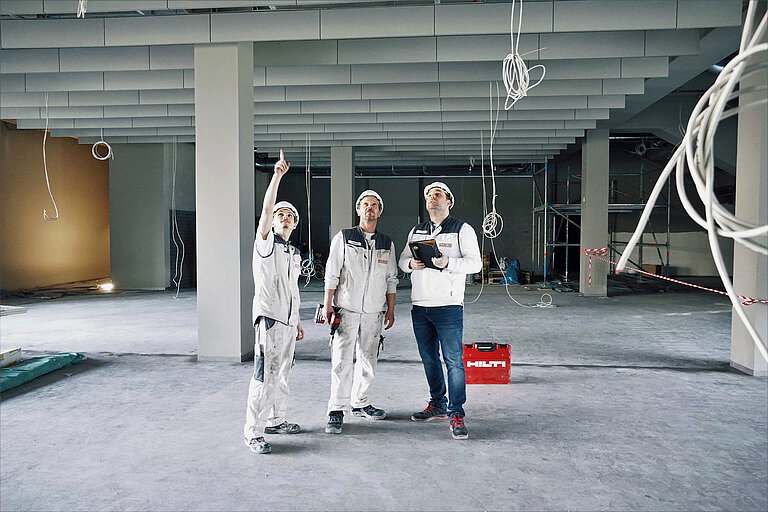
Time pressure, outdated processes, unchanged work methods and error-prone communication between the office and the construction site: Until recently, these were standard everyday problems for Frietsch Gipser und Stukkateur GmbH.
This medium-sized plastering company in southern Germany hadn’t given much thought to how it could provide a better experience for their small team of fifteen permanent employees by increasing productivity, while creating more jobs with less pressure and strain.
Before taking the reins of the company as new CEO, Christopher Frietsch didn’t know that things could change for the better. This only came after having a problem-solving consultation and seeing the automation and digitalization offered by Hilti. “With the new methods, we not only have the opportunity to advertise our company as one that is ready for the future, but also to make the skilled trades once again more attractive to school graduates,” says Christopher Frietsch, son of the founder of Frietsch Gipser und Stukkateur GmbH. He’ll be the first to tell you that it’s still early, but the initial results have excited the entire team about what the future could hold.
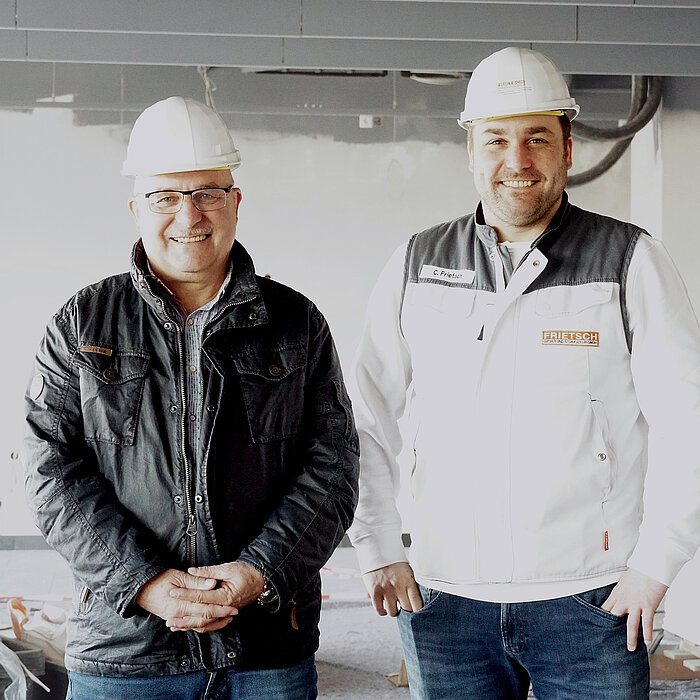
With the new methods, we not only have the opportunity to advertise our company as one that is ready for the future, but also to make the skilled trades once again more attractive to school graduates.
Christopher Frietsch, son of the founder of Frietsch Gipser und Stukkateur GmbH
“Our journey started in 2023 with a construction project to renew the stadium of Karlsruher Sport Club, a second division football club in the German Bundesliga. With the start of the interior finishing work in the hospitality areas, we were given the contract for the acoustic baffles suspended from the ceiling for sound absorption in the highly frequented areas. We were already aware of the time challenge involved when submitting our offer. During the preparation period, our Hilti consultants offered us an innovation hour where they presented Hilti innovations at our premises. We couldn’t ask for more from Hilti because we were able to directly discuss the issues we were facing with this new project,” says Christopher.
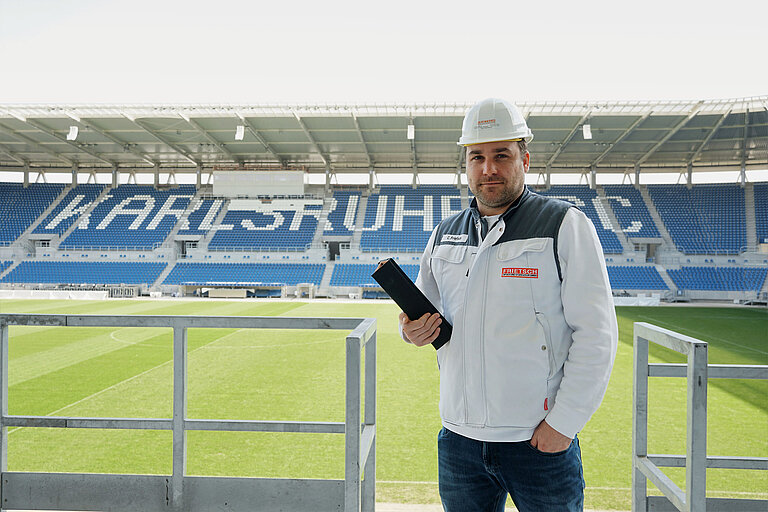
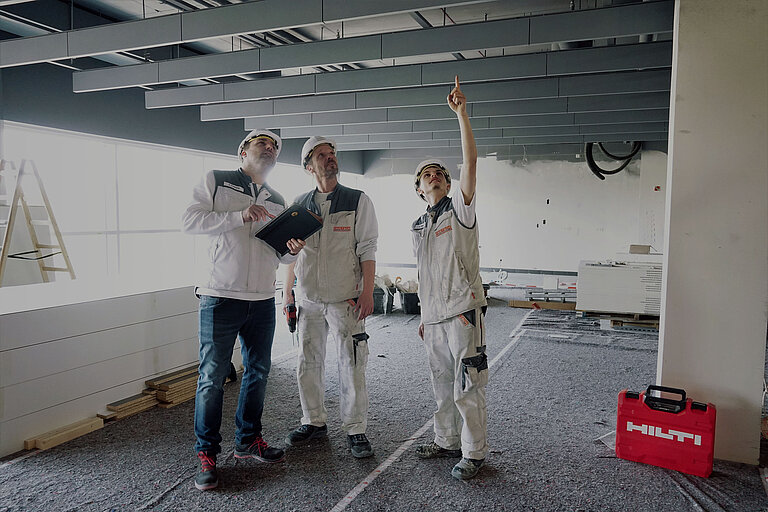
The challenges of the project were essentially threefold. First, nearly 3,000 linear meters of acoustic baffles, requiring almost 2,500 drilled holes, had to be mounted with extreme precision on a concrete ceiling that was nearly five meters high. Second, the timeline was very tight. Third, cable routes, ventilation and other obstacles were already attached to the ceiling, making it difficult to measure and drill.
Due to the high number of holes to be drilled, and in view of the tight timeframe, Lena Burkart, Hilti Sales Consultant, and Andreas Horn, Hilti Sales Manager, suggested the semi-autonomous drilling robot, Jaibot, during the innovation hour.
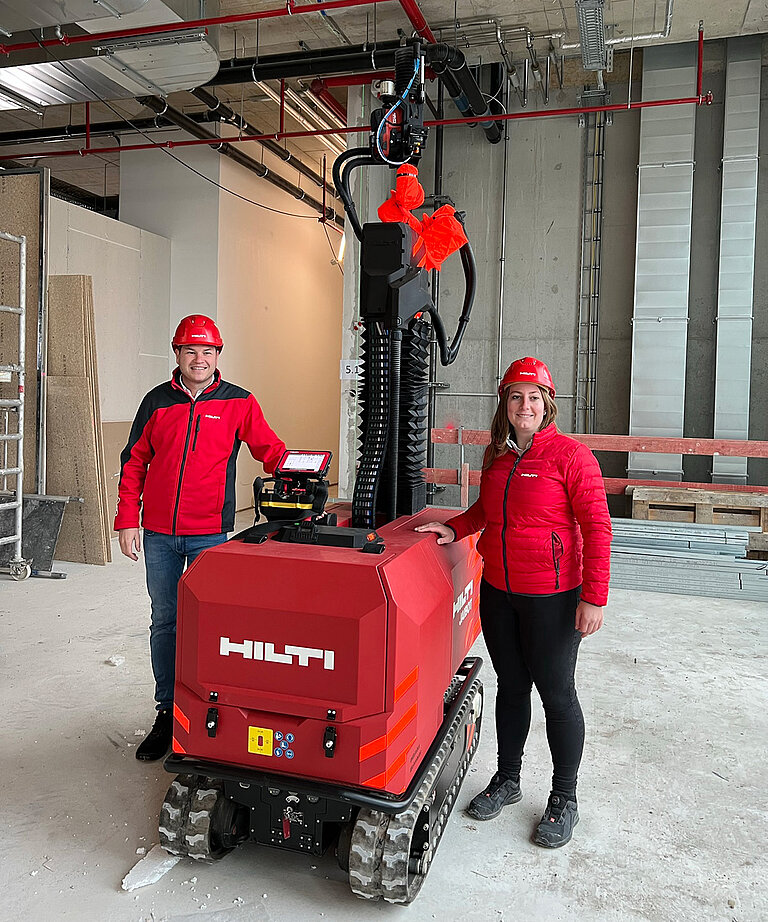
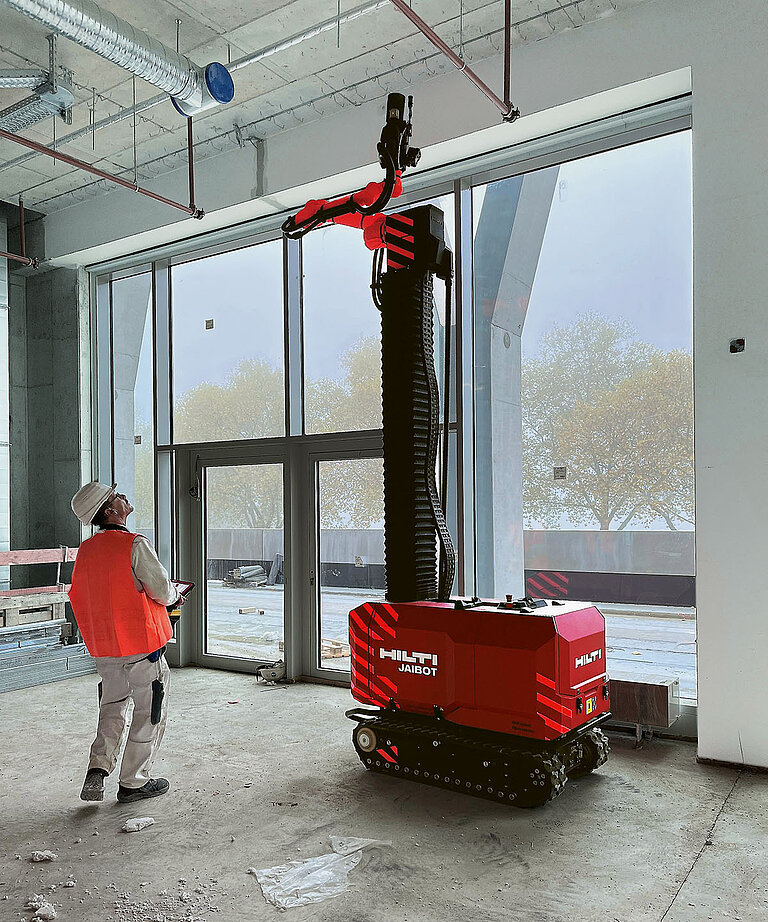
“When they told us that the Jaibot independently carries out drilling for anchor fastening points based on digital planning data, and that only one employee is needed to navigate it, we quickly decided that it would be a great help for the project and could support us in eliminating the time pressure,” says Christopher Frietsch.
Only a few weeks passed between the first conversation and the assignment. The contract was awarded sooner than expected and both the Jaibot and Hilti Jaibot Operation Manager, Benjamin Bredl, were in the Karlsruhe stadium within a few days.
“The rental offer for the drilling robot, including Hilti services in the form of data processing and importing, as well as training and support during use, was individually tailored to the project by Hilti. Hilti’s support is highly valued because they know that no project is like another. A one-day intensive training course for handling the semi-autonomous helper included a safety briefing, operation and service and maintenance. In the run-up, Hilti adapted the general contractor’s digital plans for the use of the Jaibot and inserted the required drilling points with the relevant drilling dimensions,” said Christopher Frietsch.
“Thanks to the Jaibot and PLT 300, our employees needed less muscle power and could enjoy their evenings because they were not as tired as they had previously been. That makes us much more attractive as an employer. For the Frietsch company, the enthusiasm of its fifteen permanent employees is a positive encouragement. After all, the shortage of skilled workers could also affect us on a long-term basis,” said Christopher.
“For me, this has been a completely new experience and has shown me for the first time that we, as plasterers, can also benefit from digitalization. Until now, digitalization on the construction site was an abstract concept for me and I had no idea of the areas where we could use it. I’m proud to be one of the first trainees to work with such a product. This makes the whole job description even more exciting and makes us as an employer much more attractive. I greatly look forward to the future,” says Constantin Alin Manciu, apprentice at Frietsch.
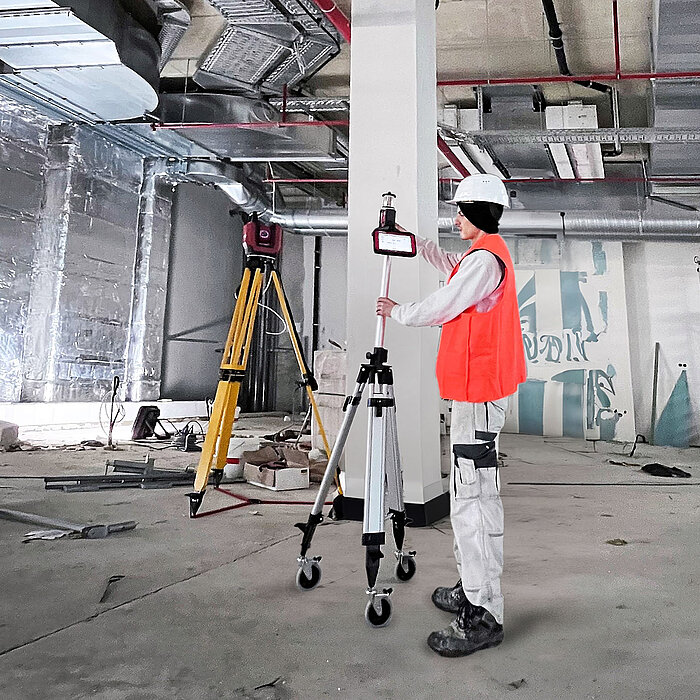
I’m proud to be one of the first trainees to work with such a product. This makes the whole job description even more exciting and makes us as an employer much more attractive.
Constantin Alin Manciu, Apprentice at Frietsch Gipser und Stukkateur GmbH
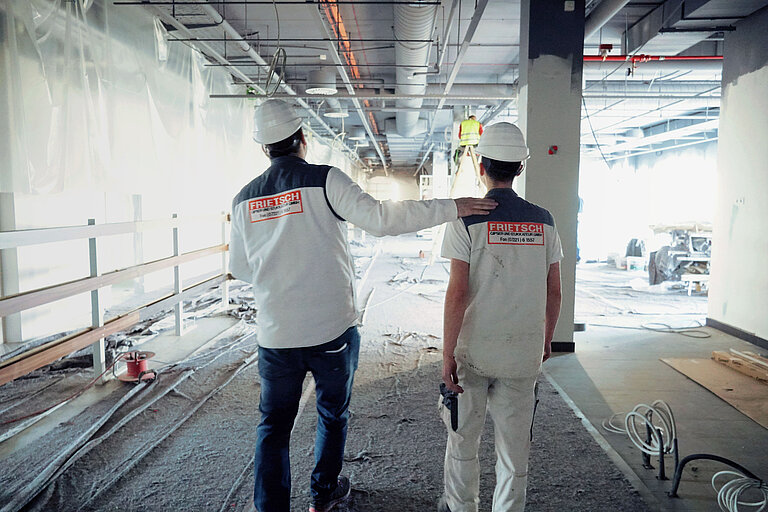
Better applications enable better construction. Discover how with Lead 2030 Hilti is Making Construction Better.